The Facts About Alcast Company Uncovered
Table of ContentsThe 9-Second Trick For Alcast CompanyThe Ultimate Guide To Alcast CompanyExcitement About Alcast CompanyThe 45-Second Trick For Alcast Company7 Simple Techniques For Alcast CompanyThe 8-Minute Rule for Alcast Company
Chemical Comparison of Cast Light weight aluminum Alloys Silicon promotes castability by lowering the alloy's melting temperature and boosting fluidity throughout casting. In addition, silicon contributes to the alloy's toughness and put on resistance, making it beneficial in applications where longevity is important, such as vehicle components and engine components.It additionally enhances the machinability of the alloy, making it simpler to refine into ended up items. In this method, iron contributes to the general workability of aluminum alloys.
Manganese adds to the strength of light weight aluminum alloys and boosts workability (Foundry). It is typically made use of in wrought aluminum products like sheets, extrusions, and profiles. The visibility of manganese help in the alloy's formability and resistance to breaking during fabrication procedures. Magnesium is a light-weight aspect that offers strength and effect resistance to aluminum alloys.
Alcast Company Things To Know Before You Get This
Zinc improves the castability of aluminum alloys and helps regulate the solidification procedure throughout spreading. It improves the alloy's toughness and solidity.
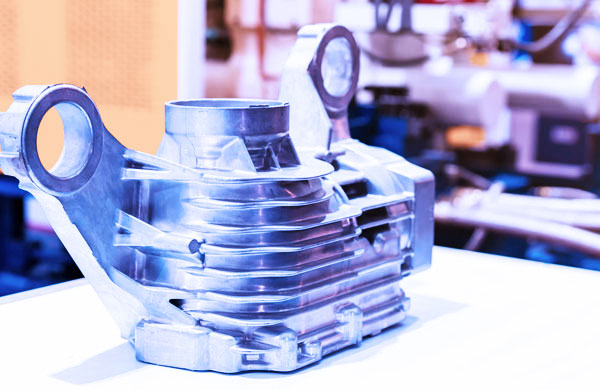
The key thermal conductivity, tensile stamina, return stamina, and elongation vary. Among the above alloys, A356 has the highest possible thermal conductivity, and A380 and ADC12 have the least expensive.
Alcast Company Fundamentals Explained
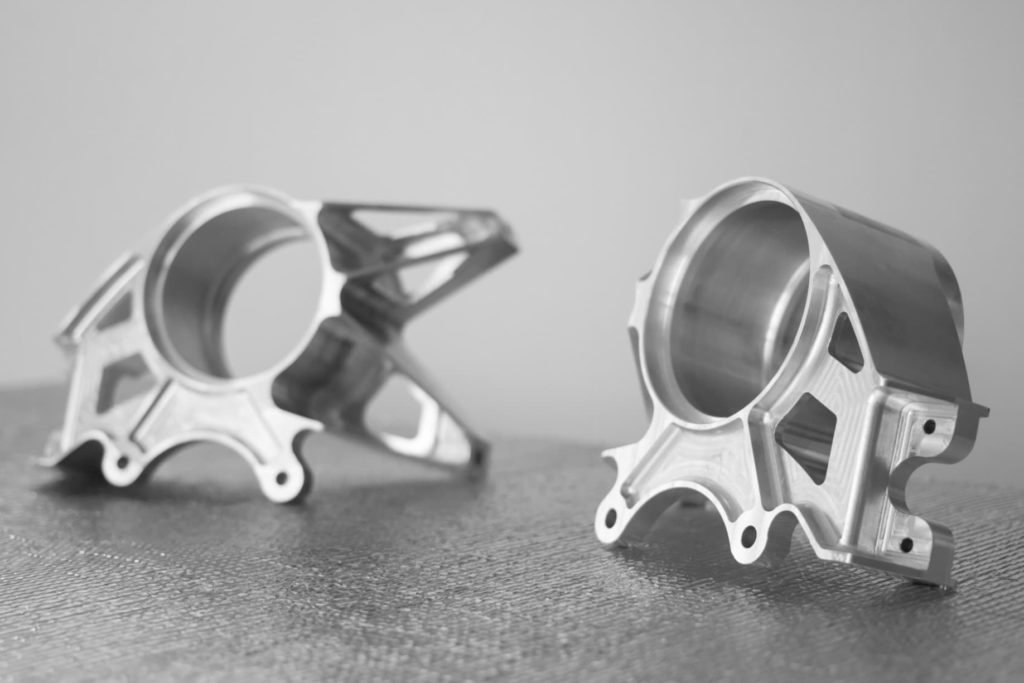
In accuracy casting, 6063 is appropriate for applications where detailed geometries and top notch surface finishes are critical. Examples consist of telecommunication enclosures, where the alloy's premium formability permits streamlined and visually pleasing designs while keeping structural honesty. In the Lights Solutions market, precision-cast 6063 elements develop elegant and effective lighting fixtures that call for detailed shapes and good thermal performance.
The A360 displays superior prolongation, making it excellent for complex and thin-walled components. In accuracy spreading applications, A360 is fit for sectors such as Customer Electronic Devices, Telecommunication, and Power Devices.
Indicators on Alcast Company You Should Know
Its one-of-a-kind homes make A360 a valuable option for precision casting in these sectors, enhancing item sturdiness and high quality. Light weight aluminum alloy 380, or A380, is a widely made use of casting alloy with several distinct features. It uses exceptional castability, making it an optimal selection for precision spreading. A380 displays great fluidness when molten, making certain complex and detailed mold and mildews are accurately duplicated.
In precision casting, aluminum 413 radiates in the Consumer Electronics and Power Equipment sectors. This alloy's remarkable rust resistance makes it an excellent option for outside applications, making sure resilient, long lasting products in the discussed sectors.
The Ultimate Guide To Alcast Company
Once you have chosen that the aluminum die casting process is suitable for your job, a crucial following action is picking one of the most ideal alloy. The light weight aluminum alloy you select will significantly impact both the spreading process and the residential or commercial properties of the end product. As a result of this, you should make your decision carefully and take an educated approach.
Identifying one of the most appropriate aluminum alloy for your application will imply considering a vast array of characteristics. These relative alloy attributes comply with the North American Die Casting Organization's guidelines, and we have actually divided them into 2 classifications. The initial category addresses alloy attributes that influence the manufacturing procedure. The second covers attributes affecting the homes of the last item.
Getting The Alcast Company To Work
The alloy you select for die casting straight influences a number of facets of the casting process, like just how very easy the alloy is to function with and if it is susceptible to casting problems. Hot breaking, also called solidification breaking, is a typical die casting issue for aluminum alloys that can result in inner great post to read or surface-level rips or cracks.
Specific aluminum alloys are a lot more at risk to hot cracking than others, and your choice needs to consider this. It can harm both the actors and the die, so you must look for alloys with high anti-soldering buildings.
Corrosion resistance, which is currently a remarkable quality of aluminum, can differ considerably from alloy to alloy and is a necessary characteristic to think about relying on the environmental problems your product will certainly be revealed to (Casting Foundry). Wear resistance is another building typically looked for in aluminum products and can set apart some alloys